
Processo que pode ser considerado novo no ramo da Engenharia, tem como vantagem a produção de protótipos
de metal plenamente densos, com boas propriedades metalúrgicas
e razoáveis velocidades de construção. A fundição do pó
metálico utilizado é feita através de um raio laser de alta
potência. O pó metálico é fornecido coaxialmente ao foco do raio laser, através de um cabeçote de deposição.
O raio laser atravessa o centro do cabeçote e é focado para um
pequeno ponto através de uma lente ou um conjunto de lentes. Uma mesa X-Y
é movida por varredura de forma a gerar cada camada do objeto. O cabeçote
é movido para cima à medida que cada camada é completada. O raio
laser pode ser conduzido até a área de trabalho através de espelhos
ou fibra ótica. Os pós metálicos são fornecidos e distribuídos ao
redor da circunferência do cabeçote por gravidade ou através de um
gás portador inerte pressurizado. Mesmo nos casos onde não se
necessitar de uma corrente de gás para se transportar o pó metálico
é necessário ter uma corrente de gás inerte para se proteger a peça
de metal líquido do oxigênio atmosférico, de forma a se garantir as
propriedades metalúrgicas e promover melhor adesão entre camadas
através de melhor molhamento superficial. São utilizados pós de
diversas ligas metálicas, tais como aço inoxidável, inconel, cobre,
alumínio e titânio. A potência do gerador de raio laser varia
conforme o material usado, taxa de deposição e outros parâmetros,
podendo oscilar desde algumas centenas até 20.000 watts ou mais. Os
protótipos produzidos requerem usinagem para acabamento, apresentando
densidade plena, boa microestrutura e propriedades similares ou
melhores ao metal convencional.
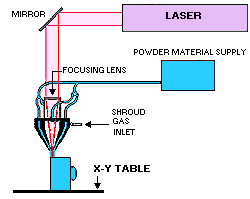

|